Overview
Flipkartās vast inventory ecosystem manages over 150 million products across 80+ categories, distributed across multiple warehouse types to cater to diverse product categories. The efficiency of inventory distribution, stock movement, and space allocation plays a critical role in reducing inefficiencies, optimizing warehouse utilization, and ensuring smooth order fulfillment
Key Metrics Analyzed
- Stock Out Variation: Indicates minimal variance in stock availability, ensuring high fulfillment rates
- Stock Inward Ratio: Measures the rate of incoming stock relative to total inventory, ensuring a balanced supply chain
- Stock Outward Ratio: Represents the percentage of stock moving out of warehouses, directly influencing order fulfillment efficiency
Warehouse Categorization & Inventory Distribution
Regular Warehouse (Mixed Product Storage)- 80-90% of inventory consists of small products, such as mobile phones, smart gadgets, and accessories
- 1-10% of inventory is allocated for large products, including refrigerators and TVs
- Electronics: 30% of total inventory
- Beauty & Personal Care: 10-15%, reflecting strong demand for fast-moving consumer goods
- 100% of inventory consists of large products, primarily home appliances, furniture, and electronics, requiring specialized handling and logistics
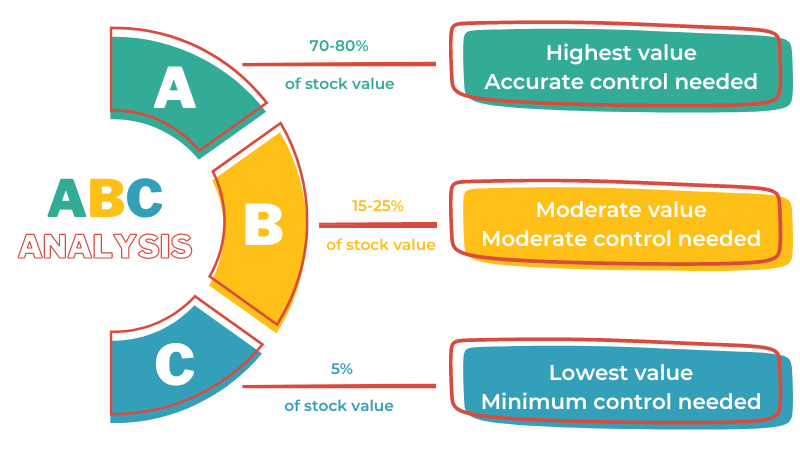
Challenges in Inventory Management
High Return Ratio in Apparel Category- Apparel has the highest return rate (10:2 orders returned) due to size mismatches, quality concerns, and customer preference shifts
- Returns impact warehouse space utilization, reverse logistics costs, and stock reprocessing efficiency
Regular stock audits are conducted to monitor inventory accuracy and reduce shrinkage. However, different categories require varying audit frequencies due to product perishability and demand volatility
- Food Products: 2-3 cycle audits per month due to shorter shelf life and quality control requirements
- Health & Beauty: 1-2 cycle audits per month to maintain stock accuracy and compliance
- Other Categories: 1 cycle audit per month, focusing on stock movement efficiency and loss prevention
- Warehouse space allocation depends on stock inward and outward volumes, making it challenging to balance fast-moving and slow-moving inventory
- Sudden demand surges in seasonal categories (fashion, electronics) require real-time space reallocation, adding operational complexity
Key Metrics Analysis & Insights
- Stock Out Variation: 0.03% PPM (Parts Per Million)
- Stock Inward Ratio: 10-15%
- Stock Outward Ratio: 5-10%
Inventory Optimization Strategies
-
Flexible Space Allocation Models:
- Adjust warehouse layout location dynamically based on real-time stock inward-outward volume trends Faster Stock Replenishment:
- Improve stock inward-outward ratio through automated inventory restocking systems
Key Outcomes & Achievements
1
Implementing dynamic space allocation based on fast movement to increase storage capacity by 15%.